
Waste Water from the Agricultural Industry
Answer our questionnaire and receive a non-binding offer
Status Quo
There are different types of wastewater on farms. A classic wastewater is the surface water on biogas plants. In addition, milking house waste water or silage effluent can be produced. All these kinds of wastewater can be treated in the FlexBio treatment plants. In addition to dischargeable water, you will be producing biogas, which you can use directly for energy.
The organic contamination of the wastewater is in the range between 200 to 15,000 mg/l COD (chemical oxygen demand). Silage effluent can even reach COD values of over 100,000 mg/L. FlexBio systems can purify low loads as well as very high loads effectively and are stable with regard to hydraulic and organic fluctuations.
Currently, wastewater is often brought into the digestate warehouse or applied to agricultural land. In the latter case, the fertilizer ordinance must be observed. It has also been shown in practice that the treatment of wastewater on the farm is the most suitable solution, as this saves the cost of deployment and storage. The compact FlexBio container units purify the waste water to direct discharging levels.
We will be happy to answer any further questions in our FAQ!

Explanation of the Technology
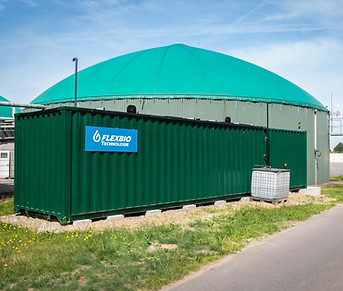
![]() |
---|
![]() |
![]() |
![]() |
![]() |
![]() |
![]() |
![]() |
![]() |
![]() |
![]() |
![]() |
The specially developed process for the purification of wastewater from the agricultural industry enables an effective reduction of the organic contamination in wastewater. The process is characterized by a compact and robust construction, as well as low energy requirements. After the treatment, the water can be reintroduced back to the natural cycle, without compromising water quality. The biogas obtained from the organic matter can be used for energy production.
In the first step, the organically contaminated liquids are effectively used in a compact fermentation plant (fixed-bed fermenter). A structured packing in this fermenter achieves a strong increase of the surface area, which serves as a colonization surface for the micro-organisms. By the fixation of the micro-organisms, a washing out is prevented and a very effective degradation of the organics can be achieved in dwelling times of under one day. The fermenter can be operated as both mesophilic and psychrophilic. The fermentation plant, like conventional biogas plants, produces biogas from the present organic matter. In addition to the elimination of organic contamination, nitrogen compounds are effectively broken down in the second step. Under aerobic conditions, the nitrification of ammonium, in part for denitrification, as well as another COD elimination, occurs in an aeration tanks downstream to the anaerobic stage . A partial flow from this stage is returned to the anaerobic fixed-bed fermenter. By the simultaneous feeding with organically contaminated wastewater, denitrification occurs under anaerobic conditions and thus the degradation of nitrate to gaseous nitrogen.
With the FlexBio process, agricultural enterprises receive an environmentally friendly, economical and flexible solution in dealing with their wastewater. By using the Biogaspotentials from wastewater (at Ø 5,000 COD mg/l up to 2 m³-methane per m³-wastewater), significant amounts of biogas can be obtained. On the other hand, the purification of the wastewater eliminates the need to transport or deploy the water volumes. This leads to the prevention of climate and environmentally damaging emissions, as well as to the reduction of road traffic in rural areas (environmental relief).
Measurement and Control Technology
The FlexBio treatment plants are equipped with state-of-the-art control and measurement technology and are designed for autonomous and fully automatic operation. Continuous measurements of relevant parameters as well as an intelligent PLC control ensure optimum utilization of the system and a safe adherence to the limit values. All settings and functions can be accessed locally as well as remotely using any smart devices (via secure VPN access). The feeding of the system is controlled according to the level in the reservoir. In addition, the organic contamination of the wastewater is measured. The recycled water can then be discharged, seeped or sprayed as required. The technical components and control elements required for the process are located in a separate machine room. In addition, the container has a status indicator (green, yellow, red), an emergency switch on the outside and a gas overload protection.
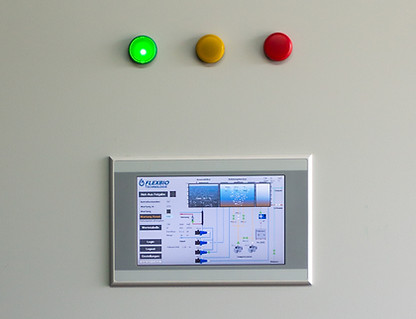
Purification Performance

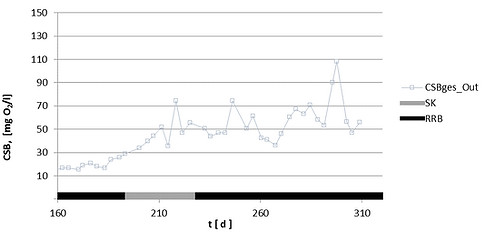
The figures show measurement parameters of a reference plant in southern Lower Saxony. Based on these graphs, the purification performance of an AFBB-010 plant (20ft container) is presented as an example. The diagrams show the organic load (COD) in the input and output of the system.
In order to demonstrate the flexibility and resilience of the purification system, 150 informative days were chosen. During this period, the plant was operated for 40 days with high-loaded silage effluent (grey section) and the remaining 110 days with slightly contaminated surface water (black section) from the rain retention basin. The input load varied between approx. 100 mg/L COD and approx. 45,000 mg/l COD. In spite of the strongly varying load, no more than 108 mg/l COD was measured in the output and no value exceeding the limit value of 120 mg/L COD was reached. The average throughput is 11 m³/d in the period indicated.
The optimum operating performance is thus continuously adjusted based on the measurements made and the associated intelligent control. Thanks to this permanent adjustment, large quantities with low load (e.g. heavy rain events) and on the other hand small quantities with a high load (e.g. silage effluent) can be treated fully automatically and effectively. In addition, the modular construction of the container systems allows an expansion by means of additional modules at any time.
Answer our questionnaire and receive a non-binding offer!